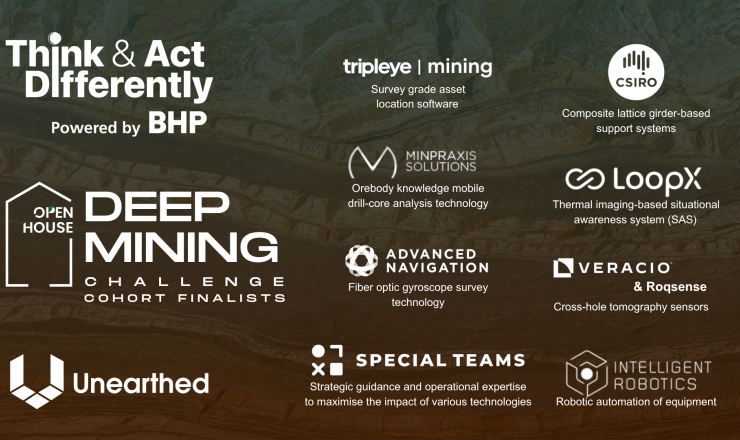
Think & Act Differently, Powered by BHP announces eight finalists for the Deep Mining Open Call
Think & Act Differently (TAD), BHP's innovation team, together with Unearthed Solutions, announced eight finalists for its Deep
Read articleThink & Act Differently, Powered by BHP (TAD), finds and accelerates the best technology solutions to support BHP’s ambitions to deliver resources the world needs in new ways. TAD uses a systems approach to foster a continuous flow of new technologies and capabilities that empower BHP to meet today’s needs and build a roadmap for future value. Using the TAD and partner innovation ecosystems, collaboration is encouraged, with a range of individuals and organisations to accelerate technologies at scale, promoting optionality, speed, and diversity.
TAD extends its thanks to Sedgman for their exceptional coordination and facilitation of the learnings from the Comminution Cohort. Their expertise and dedication were instrumental in driving the program's success and facilitating a collaborative environment that benefited all participants.
Empowering innovation through collaboration
The Think & Act Differently, Powered by BHP, Comminution Challenge was focused on finding ways to reduce energy consumption or increase throughput by delivering potential step changes in the way we crush, pulverize and grind rocks for mineral extraction. Comminution is a critical component of mineral processing operations and consumes a significant proportion of energy for processing plants.
A Cohort of twelve innovators, researchers and established vendors were selected from a global open innovation challenge run in partnership with Unearthed. Together with minerals processing solutions provider, Sedgman, the Cohort members collaborated in a three-month long study aimed at assessing and understanding the merits of various comminution technologies and their applicability to the BHP asset portfolio and other greenfield IOCG (iron oxide copper-gold) and porphyry copper ore bodies. The Cohort environment offered a platform for innovators to discuss their technologies and explore synergies and opportunities for collaboration.
The ecosystem approach to acceleration
Accelerating aspirational future comminution systems requires bringing together diverse innovators across the entire value chain. This collaborative approach is aimed at understanding the capabilities of various segments within the comminution ecosystem and envisioning what an ideal comminution system could look like.
Our approach is committed to unlocking value for BHP and our partners through an innovation and technology portfolio designed to deliver benefits today, tomorrow, and beyond.
We seek to accelerate technologies that can be implemented in current operations as step-change improvements as well as innovative combinations that form new value chains or systems that integrate multiple technologies.
We aim to cast a wide net, engaging not only traditional mining and engineering specialists, but also exploring ideas from other disciplines and industries. This inclusive approach accelerates the injection of new learnings into the innovation ecosystem.
A collaborative environment allows innovators to learn from each other, identify how their systems complement one another and pinpoint opportunities for creating value through integrated innovations. The comminution systems of the future will likely be a synthesis of various innovations spanning the entire value chain, driven by the collective expertise and creativity of the global innovation community.
"Through this cohort, we've created a comminution ecosystem through a systems approach to fast-track development and implementation of these step change technologies into our future mining operations and designs." – Ryan Bracey, Principal Process Consultant, Sedgman
Why is comminution important?
Comminution is a critical step in the field of mineral processing, which is used to reduce the size of ore particles using crushing or grinding. This process consumes a large proportion of energy required for mining and mineral processing. For example, considering an open pit copper concentrator, comminution requires over a third of the mine’s electrical energy to operate, as shown in the diagram below. By optimising energy efficiency within comminution through novel comminution technologies, the site energy consumption can be reduced or production rate increased.
A well-designed comminution technology should require less specific energy (energy per tonne of ore processed) to process ore and/or produce improved liberation of valuable minerals. This will likely result in upstream and downstream optimisations to occur, requiring less energy and water, and increasing product quality and quantity. Current comminution technologies, such as jaw crushers, gyratory crushers, cone crushers, SAG mills, and ball mills, are used across the globe in a range of different processes. These technologies are reaching physical limitations regarding energy consumption, liberation and throughput. Therefore, novel comminution technologies which provide improvements in energy consumption, water consumption, or improved liberation are being investigated to determine their validity and to provide support to innovators to assist in technological and commercial development.
Novel comminution global trends
Significant development is taking place on a global scale in novel comminution and sorting technologies, and this was clearly evidenced through over 35 individual company innovator submissions to the TAD Comminution Challenge. The range of technologies presented by innovators globally covered a wide range of applications and industries. The Cohort submissions all shared a common ambition: to transform the industry through innovation and optimisation of the current operational norms.
We saw a range of mechanical comminution technologies that focused on optimised energy delivery to ore and significantly reducing operational costs including energy and media use. Several innovators focused on early waste rejection from the system with varied approaches to sorting and pre-concentration technologies. Established technologies in parallel industries were also a theme within the Cohort, which enabled an accelerated development path into the mining sector and its challenges. The technologies being de-risked had various goals they wanted to achieve, including operating without grinding media, to save over 80% energy, dry processing and early waste rejection.
Across the Comminution Cohort, transforming the industry was an aspirational objective. TAD, with its systemic approach to innovation, is striving to expedite the integration of transformation technology into the sector, ultimately paving the way for the concentrator of the future.
Comminution Cohort - program objectives
The objectives for this study were to evaluate novel comminution technologies in a systematic manner against BHP technologies key drivers. Specifically, this included:
- Review the viability of the technology’s fundamental properties in the context and scale of mining from a process, mechanical, and materials handling viewpoint including comminution breakage mechanisms, operational characteristics and performance characteristics (water and energy).
- Review potential issues and concerns, including potential mechanical, performance issues or safety considerations. - Review capital and operating estimates at a high-level using data provided by the innovators. - Compare the comminution technologies, identifying development opportunities for each, including opportunities to integrate multiple technologies in novel comminution flowsheets.
An important objective was to provide a forum for the innovators to connect and discuss their solutions, with the aim to look for synergies and opportunities for further collaboration within the group.
Summary Highlights
The program brought together deep experts and innovators with novel ideas. One of the most significant outcomes was the willingness of innovators to collaborate, despite initial concerns that potential competitors might not want to share information. To accelerate their technologies, innovators were eager to understand the real competitive environment and the long-term viability of their technologies, leading to an unprecedented level of cooperation.
This way of working enabled the Cohort to rapidly build a robust understanding of where new technologies could be applied, how they can be integrated into flowsheets and what needs to be true for them to work commercially. This collaborative and rapid approach significantly exceeded the potential outcomes of teams working independently. It is unlikely that traditional studies would have achieved such beneficial outcomes, clearly demonstrating the high value of open collaboration and an abundance mindset. Overall, the process potentially created more commercial opportunities for all companies involved, as they collectively unlocked new approaches to solve high-value problems.
A valuable highlight of the Comminution Cohort is the potential for different technologies to synergistically work together, enhancing overall processing efficiency and outcomes. The distinct yet complementary nature of each technology within the Cohort offers a unique opportunity to integrate and optimise processes. It is likely that comminution processes of the future will be a blend of different technologies that contribute to an advanced system. The knowledge gained from collaborating with diverse external partners has formed a robust business case for recommendations and investment decisions.
Another highlight was that several innovators leveraged the collaborative Cohort and involvement with subject matter experts to refine their development pathways. For example, as a result of subject matter expert feedback, GRolls® pivoted their research and development to better align with typical operating parameters and targets. This adjustment allowed for more efficient processes and increased the likelihood of commercial success.
In light of global trends in mineral demand and decreasing grades, innovative comminution technology has gained significant traction to address these challenges. This is evidenced by the impressive submissions to the Cohort and the international presence of each innovator within it, underscoring the global market and the value these technologies seek to address.
The Comminution study has been successful in demonstrating that collaboration and learning are key to accelerating technological advancements. Both BHP and the participating innovators have gained valuable insights and forged strong partnerships that will continue to drive innovation in the industry. We look forward to building on this momentum and exploring new opportunities for collaboration and growth.
Innovators involved in the Comminution Cohort
Unearthed were our open innovation challenge partner and the following innovators participated in the Comminution Cohort Program:
• University of Nottingham – Selective Heat Ore Treatment (SHOT)
• NaturaFrac – Pulsed dynamic in-situ pre-conditioning
• SMI-JKMRC – High Voltage Pulse (HVP)
• ReThink Milling Inc. – Conjugate Anvil Hammer Mill (CAHM)
• Gyratory Roller Solutions – GRolls®
• Green Earth Technologies – The Revolution Mill
• Disa Technologies – High Pressure Slurry Ablation (HPSA)
• Sharp Pulse Corporation – Sharp Pulse Plasma Power Technology
• Rockburst Technologies – RockBurst transcritical CO2 comminution
• Weir Minerals – HPGR with Air Classification
• Comminution Reimagined – ARBS mill
• EDS – Multishaft Mill
Each of these innovators brought unique perspectives and diverse technologies that contributed to the program's success. The review of these technologies was completed through a multi-criteria analysis, focusing on key themes. The MCA themes which underpinned the review were:
• Environmental, social and safety
• Mechanical, materials handling and electrical
• Process
• Technology readiness
A forward work plan is being determined to accelerate comminution options with the potential of accelerating some technologies to pilot demonstrations. This will enable TAD to quantify the applicability of these technologies to BHP assets.
Multishaft Mill – EDS
The EDS Multishaft Mill is a novel comminution device which has been developed by Energy and Densification Systems, South Africa. The Multishaft Mill contains a series of shafts with opposing flingers that rotate towards one another. This increases particle-particle interactions, causing them to reduce in size by impacting against each other. The mill is fed through the top opening via conveyor and the discharge is controlled through an adjustable flop gate on the bottom of the mill, which can open and close rapidly based on power draw within the latter stages of the mill. The mill contains multiple stages, providing high energy impacts and controllable discharge gates that enable retention time to be varied to control the product particle size.
The EDS Multishaft Mill has been recognised as an enabling technology for a number of other technologies within the Cohort, due to its unique processing range. Several new flowsheet configurations have been proposed to the EDS team to specifically target different ore types. This technology integrates well with other novel comminution technologies and provides an opportunity to integrate with novel flotation technologies to maximise the preferential liberation benefit.
There have been so many great learnings in the Cohort, there are so many technologies out there and it's great to see that innovation coming into one of the most conservative industries – Boaz Friedland Technical Director, EDS
HPGR with air classification – Weir Minerals
The HPGR and dry air classification is a comminution technology that has been developed by Weir. It combines High-Pressure Grinding Rolls (HPGR), which is a known technology to the mining industry, with dry air classification in a closed circuit. The HPGR, uses two rollers to apply pressure to the particles from multiple directions, resulting in inter-particle grinding. The HPGR rollers are pressure controlled, rather than traditional gap controlled seen in jaw and gyratory crushers. This allows pressure to be transferred to the particles via multiple directions, causing breakage and fracturing as the compressive strength is exceeded. The HPGR with Air Classifier is currently operating in a commercial operation but still requires some optimisation specifically for hard rock copper ore, particularly in combination with concentration technologies.
The HPGR and air classification technologies are proven, at scale, in iron ore. The integration of the air classification unit enables the benefits of the HPGR grinding mechanism to be applied across a larger size range than a typical HPGR screening application. The cohort experience provided insights for collaboration and new circuit configurations utilising multiple technologies.
ARBS Mill – Comminution Reimagined
The Accurate Rock Breakage System (ARBS) mill is a dry comminution technology that was developed by Comminution Reimagined. The technology comminutes material at low power compared to conventional comminution equipment. The technology has continuous pilot-scale operations and is showing excellent results in terms of energy use and reduction ratio across the unit. The breakage mechanism could lead to selective breakage allowing early sorting and coarse particle flotation opportunities to minimise water and energy, whilst maximising recovery of valuable minerals.
The ARBS mill has great potential as a novel comminution device for low energy and low water consumption. This technology provides significant opportunities to target multiple ore types and provide value. The mill also aligns with sorting and other novel technologies within the Cohort to add overall circuit value.
Conjugate Anvil Hammer Mill (CAHM) – Re-Think Milling
The Conjugate Anvil Hammer Mill (CAHM) by ReThink Milling Incorporated is a novel comminution technology based on the efficiency research of Professor Klaus Schönert. The technology operates using an inner roll (hammer) that rotates synchronously with an outer shell (anvil). The hammer and anvil both have a liner with intermeshing grooves that run radially along the surface. The anvil wheel contains discharge slots around the surface, allowing undersize material to discharge from the unit. A single drive motor with gearbox is used to drive both the hammer and anvil using split output shafts. The CAHM is a dry process, with anticipated energy improvements and 50 t/h pilot scale unit developed at the Quebec facility, Canada.
The CAHM is an exciting technology with a proven breakage mechanism. It's a dry comminution device which links with other novel comminution technologies and utilises low energy. The Re-Think Milling program, that BHP is involved in, provides a mechanism for fast-track development of technologies including the CAHM.
We share with many of our Cohort members an aspiration to eliminate grinding media entirely from SAG and ball mills – Steve Wilson CTO, Re-Think Milling
Gyratory Rolls (GRolls)
The Gyratory Rolls Crusher (GRolls®) has been developed by Gyratory Roller Solutions Pty. Ltd. in South Australia. The unit comprises two rollers, a “V” profiled main rotating roller, and an intermeshing “V” profiled oscillating roller. The chevron roller configuration provides multiple crushing chambers for wet and dry feed materials within a single unit. The GRolls is a lower TRL technology with a single alpha prototype located at the University of South Australia. This unit is designed to process wet or dry feed material and is aimed to reduce energy consumption based on the breakage mechanism. The technology is currently laboratory scale but has a clear development pathway with multiple collaborators involved.
The technical team at GRolls leveraged the collaborative Cohort and involvement with subject matter experts to refine development pathways and, as a result, pivoted their research and development to align with more typical operating parameters and targets.
Being a part of the Cohort has been very informative as we've seen the long development process for each innovator and being part of this helps us understand those challenges - Mark Drechsler Director GRolls.
High-Pressure Slurry Ablation - Disa Technologies
High-Pressure Slurry Ablation (HPSA) is a comminution technology developed by Disa Technologies located in Wyoming, USA. The technology utilises high pressure slurry streams colliding with each other to liberate minerals from gangue. The technology has been utilised in varying applications including lab-scale batch programs, pilot programs, and small demonstration units in operational environments.
The HPSA technology presents a low energy, preferential liberation technology which has been well proven in other industries and commodities. The modular design of the technology enables easy integration into operations, along with rapid startup and shutdown. This technology integrates well with other novel comminution technologies and provides an opportunity to integrate with novel flotation technologies to maximise the preferential liberation benefit.
We found that collaboration was much greater than we perhaps had anticipated, and we see the ability to work with complementary technologies, which we've started to explore already – Sam Palombo VP Business Development, Disa Technologies
Big Green Mill – Green Earth Global
The Big Green Mill produced by Green Earth Global is a vertical gyroscopic attrition milling machine. The technology uses a low energy drive to rotate the internal blades at significant velocities to produce vortices inside the unit causing particles to accelerate which then collide with each other and/or the blades. This results in high impact energies causing attrition milling of the particles as well as shear forces within the particles due to rapid direction changes. The mill operates dry and does not require grinding media. The Big Green Mill is proven in an integrated system in industrial material recycling and processing and is now being re-engineered for the mining industry.
The Big Green Mill presents a high-speed vertical mill which has proven ability in the recycling industry. Its development into hard rock minerals processing will require test-work and additional sampling to be completed. The mill operates dry and has the potential for a large reduction ratio with minimal energy consumption, enabling integration with other technologies.
Sharp Pulse Plasma Technology – Sharp Pulse
The Sharp Pulse technology is an in-line, continuous pulse plasma technology developed by Sharp Pulse Corporation, based in the United States. By applying a high-voltage pulse across the ore, the technology is designed to generate fractures along the grain boundaries between the valuable mineral and gangue. This is due to differences in the permittivity and conductivity of different minerals present in the ore, causing expansion of certain minerals. This applies tensile and compressive forces within the particle, resulting in the formation of fractures. The technology has been tested using a laboratory scale prototype on different minerals to generate process performance data and design data for a small continuous system.
Sharp Pulse electrical comminution technology operates on a proven breakage mechanism, which can result in preferential liberation. The Sharp Pulse team is experienced in pulse plasma research and technology, which will fast-track their technology development over the coming years. Although laboratory scale, electrical comminution technologies are well suited to deliver value into processing circuits.
A great opportunity to be involved and learn about BHP and other comminution technologies. Our mission is to save 1 Gt of CO2 emissions by advancing pulse plasma technology for sustainable minerals processing – Alexey Gavrilenya, CEO Sharp Pulse.
Transcritical carbon dioxide comminution – RockBurst
The RockBurst technology, developed by Rockburst Technologies in Vancouver, utilises supercritical carbon dioxide (CO2) to break material under tension. Raw feed ore contains cracks, cavities, and grain boundaries that under pressure, supercritical CO2 can enter. When material is rapidly decompressed, the CO2 changes from supercritical to saturated and volumetrically expands. The force generated from the CO2 expansion applies tensile stress on the material and causes it to break. The innovator has constructed an alpha laboratory prototype and conducted testing on a range of different materials.
The team at RockBurst is aiming to exploit the low energy requirements of tensile breakage whilst also investigating carbon sequestration opportunities. The technology has been demonstrated on copper ores and the future development will focus on optimising the unit and expanding the scale.
Ex-situ microwave conditioning – SHOT
The Selective Ore Heat Treatment (SHOT) technology is an ex-situ microwave conditioning system developed by the University of Nottingham, Jenike & Johanson, and Bear Rock Solutions. The unit is designed to apply high-intensity microwave energy directly to minerals, causing differential heating to generate thermal stresses primarily at grain boundaries.
The SHOT technology has a continuous, pilot scale unit, capable of 150t/h operation on various ore types. The technology can preferentially liberate particles due to the differential thermal expansion within particles. Given the processing characteristics of the unit, it can also integrate well with other novel technologies to provide further circuit value. Quantifying the preferential liberation through upcoming test work will define this technology’s value add to a processing circuit.
SHOT is a rapid volumetric and selective heating mechanism that heats up predominantly sulphide minerals, so we're really trying to fundamentally alter the way that the ore will fracture - Andrew Batchelor, Research Fellow University of Nottingham
Pulsed dynamic in-situ preconditioning – NaturaFrac
Pulsed Dynamic In-Situ Preconditioning is a technology that has been developed by NaturaFrac from Liberty Lake, Washington, USA. The technology uses surface injection of reactive gases and subsequent subsurface dynamic pulsed detonation-based combustion to generate a variety of desirable fracture responses in the stope or bench. The NaturaFrac technology has been tested at laboratory scale, with several simulations also completed.
NaturaFrac's technology is centred around the vast opportunity to increase fracturing upstream of the processing plant. The technology aims to increase fracturing and reduce particle size to be processed downstream, saving energy and increasing value. Current simulation and early test work shows promising results for the technology and the team from NaturaFrac have received benefit from the collaborative environment and experts involved to assist with the next stages of their development.
The preconditioning process is tuneable to where we can achieve different types of fracture architectures depending on what the what the target is, reducing downstream energy requirements in the mine – Jacob Anderson CEO, NaturaFrac
High Voltage Pulse – SMI-JKMRC
The High Voltage Pulse (HVP) Electrode Grizzly system is a high voltage electrical pulse technology developed by the Julius Kruttschnitt Mineral Research Centre (JKMRC), part of the Sustainable Minerals Institute (SMI) at the University of Queensland. The technology utilises short-rise time electrical discharges applied through a dielectric fluid to generate electrical streamers, akin to lightning, that selectively target mineralised ores, causing breakage at the mineral-gangue grain boundaries.
The HVP has currently demonstrated semi-continuous tests at laboratory scale, with plans for expansion of this design to a larger scale. The HVP is a well-established electrical comminution technology which also includes a sorting/upgrade process. The development of this technology has seen great results for ore preconcentration and pre-weakening, reducing downstream processing requirements. The HVP's development will continue through Trailblazer research funding initiatives.
Key takeaways
The desktop study yielded positive results for each of the innovators that participated in the TAD Cohort. The study has highlighted the key technologies which can create a step change in the industry.
The cohort program fostered collaboration and has highlighted potential opportunities between several innovators with complementary technologies that continue to work together.
Technology synergies fostered the creation of future flowsheets, combining multiple novel technologies for a fundamental change in water and energy use.
Collaboration with internal and external technical experts has assisted technologists to pivot and direct their future efforts to maximise value generation and technology development.
Innovators were each provided forward work plans with detailed ideas and options to progress their technology in line with their specific multi-criteria analysis outcomes.
Collaboration, thought leadership and an overarching systems approach will enable fast-tracked fundamental changes to our industry.
Read the original report here.